耐腐蚀热油泵作为工业流程中的关键设备,在化工、石油、制药等行业中扮演着重要角色。然而,在输送高温、腐蚀性介质时,热油泵面临着严峻的材料退化挑战。腐蚀不仅会降低设备效率,增加维护成本,更可能导致安全隐患。因此,对耐腐蚀热油泵进行全面的防腐蚀结构优化,从叶轮到轴承系统,成为提升设备可靠性和使用寿命的关键所在。
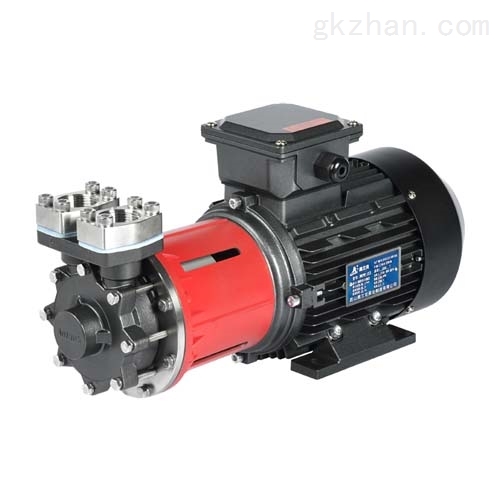
一、腐蚀问题概述
耐腐蚀热油泵在运行过程中主要面临三种腐蚀机制:化学腐蚀、电化学腐蚀和冲蚀腐蚀。化学腐蚀源于介质与金属材料直接发生的氧化还原反应;电化学腐蚀则是由于金属表面形成原电池而产生的局部腐蚀;而冲蚀腐蚀则是流体机械作用与化学腐蚀共同作用的结果。这些腐蚀形式往往相互促进,加速材料失效。
腐蚀对设备性能的影响是多方面的。首先,过流部件表面粗糙度增加导致水力效率下降;其次,材料损失会造成机械强度降低,影响运行安全性;再者,腐蚀产物可能污染介质,影响产品质量。
二、叶轮系统的防腐蚀优化
叶轮作为热油泵的核心过流部件,其防腐蚀设计尤为重要。材料选择上,双相不锈钢(如2205)表现出优异的耐蚀性能,其PREN(耐点蚀当量)值超过35,能有效抵抗氯化物应力腐蚀开裂。对于更苛刻的工况,哈氏合金C-276是理想选择,其在高温强酸环境中仍能保持稳定。
结构设计方面,采用后弯式叶片可降低流速,减少冲蚀风险;增加叶片进口边厚度(通常为普通设计的1.2-1.5倍)能延长使用寿命。表面处理技术中,高速氧燃料(HVOF)喷涂碳化钨涂层可使叶轮耐蚀性提升3-5倍,而激光熔覆技术能在关键部位形成冶金结合的耐蚀合金层。
三、轴承系统的防腐蚀创新
轴承系统在腐蚀环境下面临挑战。传统油脂润滑易被介质污染,导致润滑失效。解决方案包括采用密封的陶瓷轴承(如Si3N4),其耐腐蚀性是钢制轴承的10倍以上,或使用特殊合金轴承(如蒙乃尔K500)。润滑系统革新方面,磁力耦合隔离技术可隔绝介质接触,而采用全氟聚醚(PFPE)基润滑脂能在300℃高温下保持稳定。
辅助措施包括在轴承箱内充入惰性气体(如氮气)形成正压保护,以及安装在线腐蚀监测传感器,实时监控轴承状态。数据显示,这些措施可将轴承寿命延长至传统设计的2-3倍。
四、综合优化与未来展望
将叶轮与轴承系统优化相结合,需考虑整体协调性。例如,叶轮材质选择应兼顾与轴承材料的电化学相容性,避免形成电偶腐蚀。
未来发展趋势包括智能防腐系统的应用,如基于物联网的腐蚀速率实时监测;自修复材料的研发,如含有缓蚀剂微胶囊的涂层;以及3D打印技术实现复杂防腐蚀结构的一体化制造。这些创新将进一步推动耐腐蚀热油泵耐腐蚀性能的突破。